K.U.S Aluminium Formwork has attained band 2 with a total of 14 points in constructability under Buildable Design Appraisal System (BDAS) assessment which is conducted by Building and Construction Authority (BCA) in Singapore. This signifies the highest banding awarded for vertical and horizontal integrated small panelled.
Monoset – Aluminium Formwork
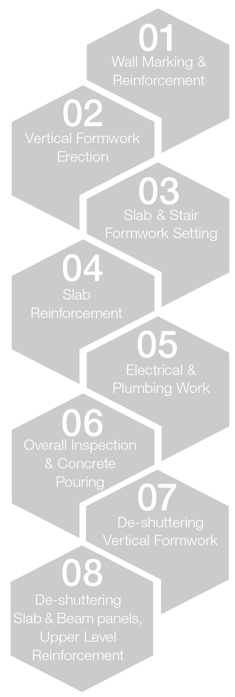
PREPARATION BEFORE INSTALLATION
- The Set up lines are drawn according to the structural drawing
- Check and assess all formwork system’s components
- Intensive cleaning of concrete residues if panels and accessories are used for the previous projects
- Panels must be applied with sufficient form oil
- Safety and installation brief need to be conducted for the site team
PRE-CHECK BEFORE CASTING OF CONCRETE
- Countercheck the position of the walls and columns with the set up marking
- Vertical and horizontal level of wall and slab must be checked
- Ensuring pins, wedges and ties are properly tightened
- Confirm the opening dimensions
- Inspect the height of all support
- Adequate bracing to ensure stability
MONITOR DURING CASTING
- Concrete pouring is distributed throughout all wall sections before commencing to cast slab areas
- Monitor cement slurry leakage
- Immediately remove/clean all excess concrete that is stuck on the back of formwork
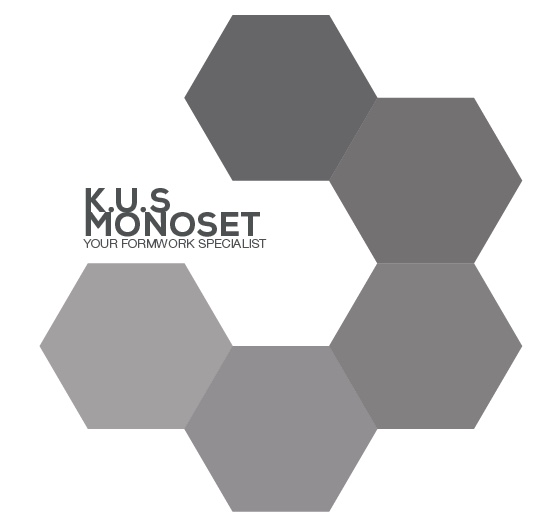
SPEED
Due to its monolithic system, construction speed increases and it takes around 8 to 10 days to construct a single floor. With same number of workers, contractor will expect the output to be double or triple when converts from conventional formwork system to aluminium formwork system.
COST REDUCTION
Due to its easiness of assembly, skilled workers are not required and monolithic concreting results in crack free structure. As such, extra repairing costs are saved and initial cost is further reduced with high repetitive usage.
QUALITY & DURABILITY
Having Aluminium alloy (A6061-T6) as the material yield its repetitive use up to 250 times. Moreover, due to the smooth surfaces and dimensional accuracy in the panels, plastering and remedial works are not required after concrete casting.
REDUCED NUMBER OF SKILLED WORKERS
The assembly of aluminium formwork system is simple and convenient. It can be assembled manually without any machines assistance. Long training hours are not required for non skilled construction workers. A simple half day training is sufficient for the non skilled constuction workers to understand the system.
ALL IN ONE SYSTEM
Aluminium Formwork system provides wide range of applications, from wall formwork, horizontal floor slab, columns, beams to stairs. It also has high recycling value that is friendly and safe to the environment.
Characteristics | Tunnel Formwork |
Table Formwork | Traditional Formwork | Aluminium Formwork |
---|---|---|---|---|
No Skilled labour required | ✓ | |||
Suitable for one or two Storey building | ✓ | ✓ | ✓ | ✓ |
Suitable for High rise building | ✓ | ✓ | ||
No cranes or other heavy equipments required | ✓ | |||
Able to pour all walls, beams, columns, slabs together along with staircase in one pour | ✓ | |||
Able to formall concrete elements | ✓ | ✓ | ||
Strike floor slab formwork without moving props and prop heads | ✓ | |||
Conforms to architect design with no need of modification to suit the design accurately or perfectly | ✓ | ✓ | ||
Self correction feature providing unmatched forming accuracy | ✓ | |||
Environmental friendly – no huge debris, no messy disposals | ✓ |
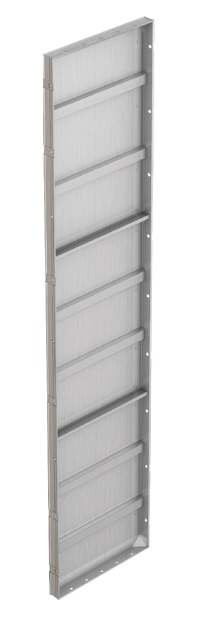
The most important aspect of a successful structural construction is the formwork system. K.U.S formwork will always offer you the most trustworthy, secure, efficient and cutting edge of formwork system techology available in the market.
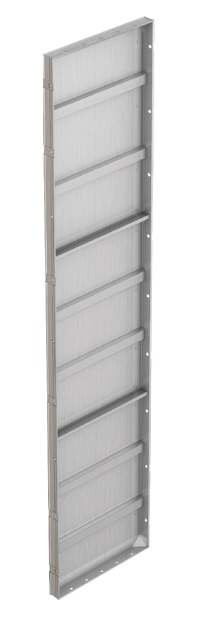
Description | Dimensions |
Standard Wall Panel | 600mm x 2400mm (H)* |
450mm x 2400mm (H)* | |
200mm x 2400mm (H)* | |
175mm x 2400mm (H)* |
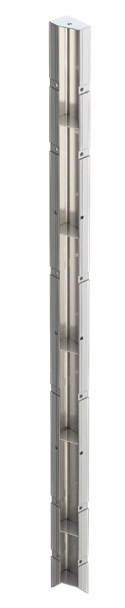
Description | Dimensions |
Standard Wall In-Corner Panel |
(100mm + 100mm) x 2450mm (H)* |
(100mm + 125mm) x 2450mm (H) | |
(100mm + 150mm) x 2450mm (H)* | |
(75mm + 125mm) x 2450mm (H)* |
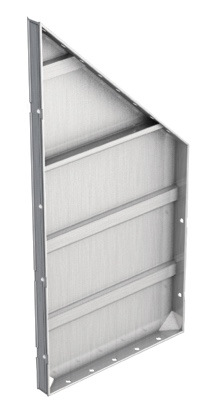
Description | Dimensions |
Angle Wall Panel | 600mm x (H)* |
450mm x (H)* | |
200mm x (H)* | |
175mm x (H)* |
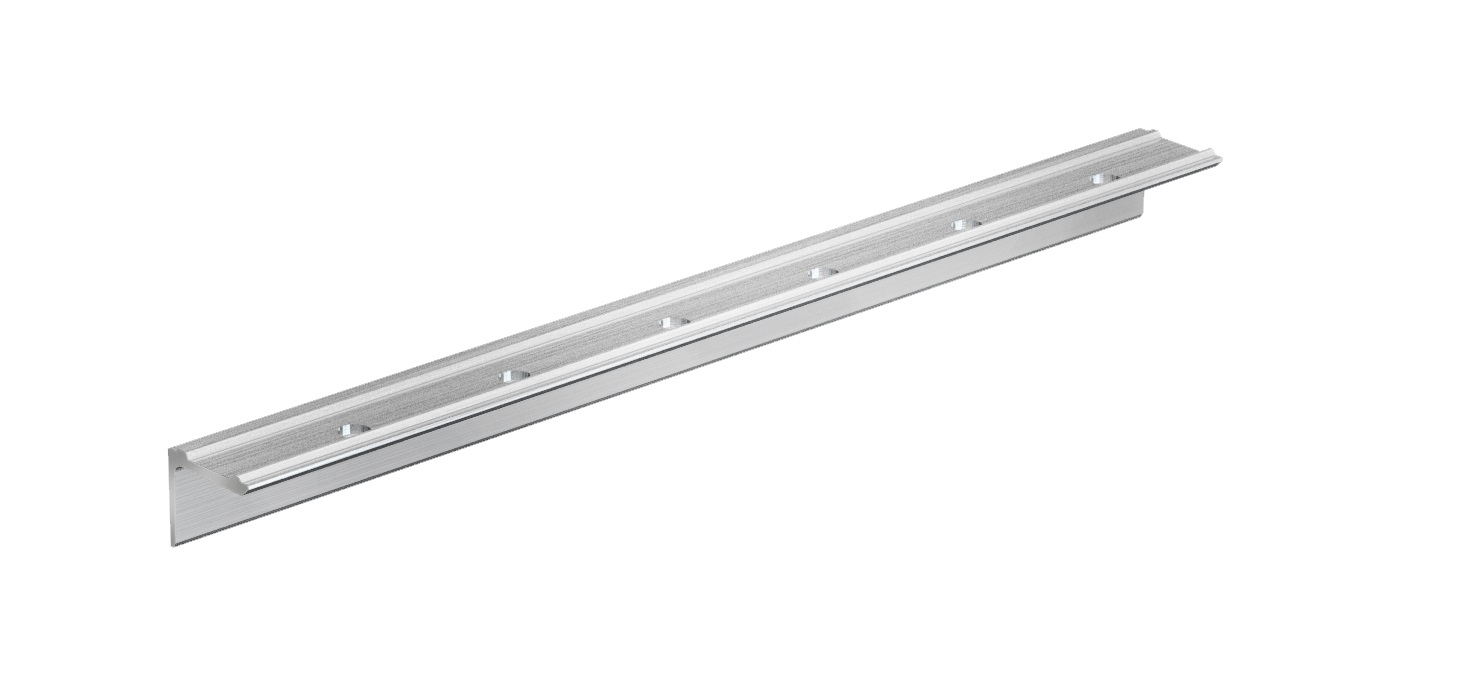
Description | Dimension |
Rocker | 50mm + 60mm x (W)* |
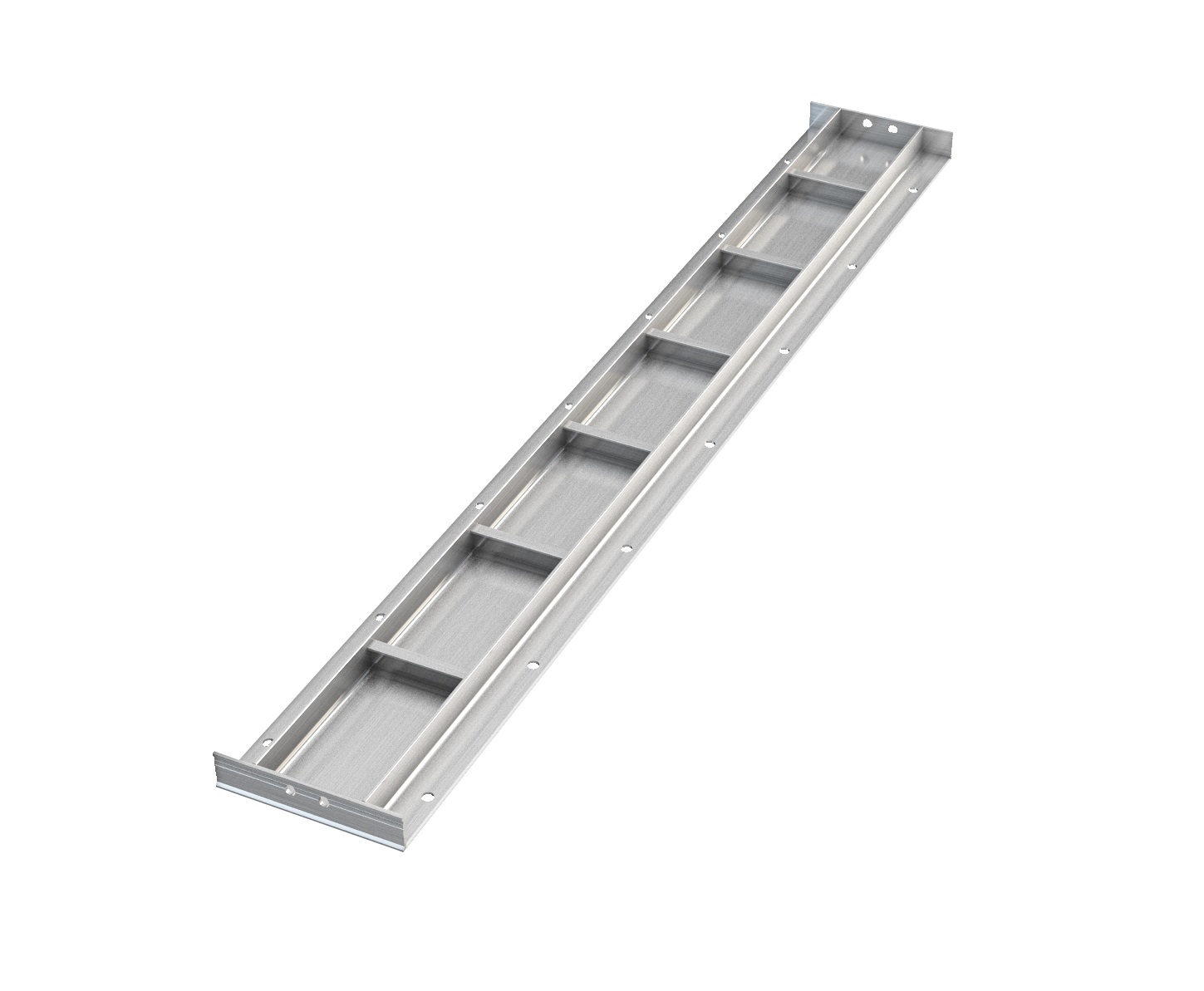
WALL END PANEL is used to sustain the weight of concrete during casting and covers a scalloped edge space where two panels meet.
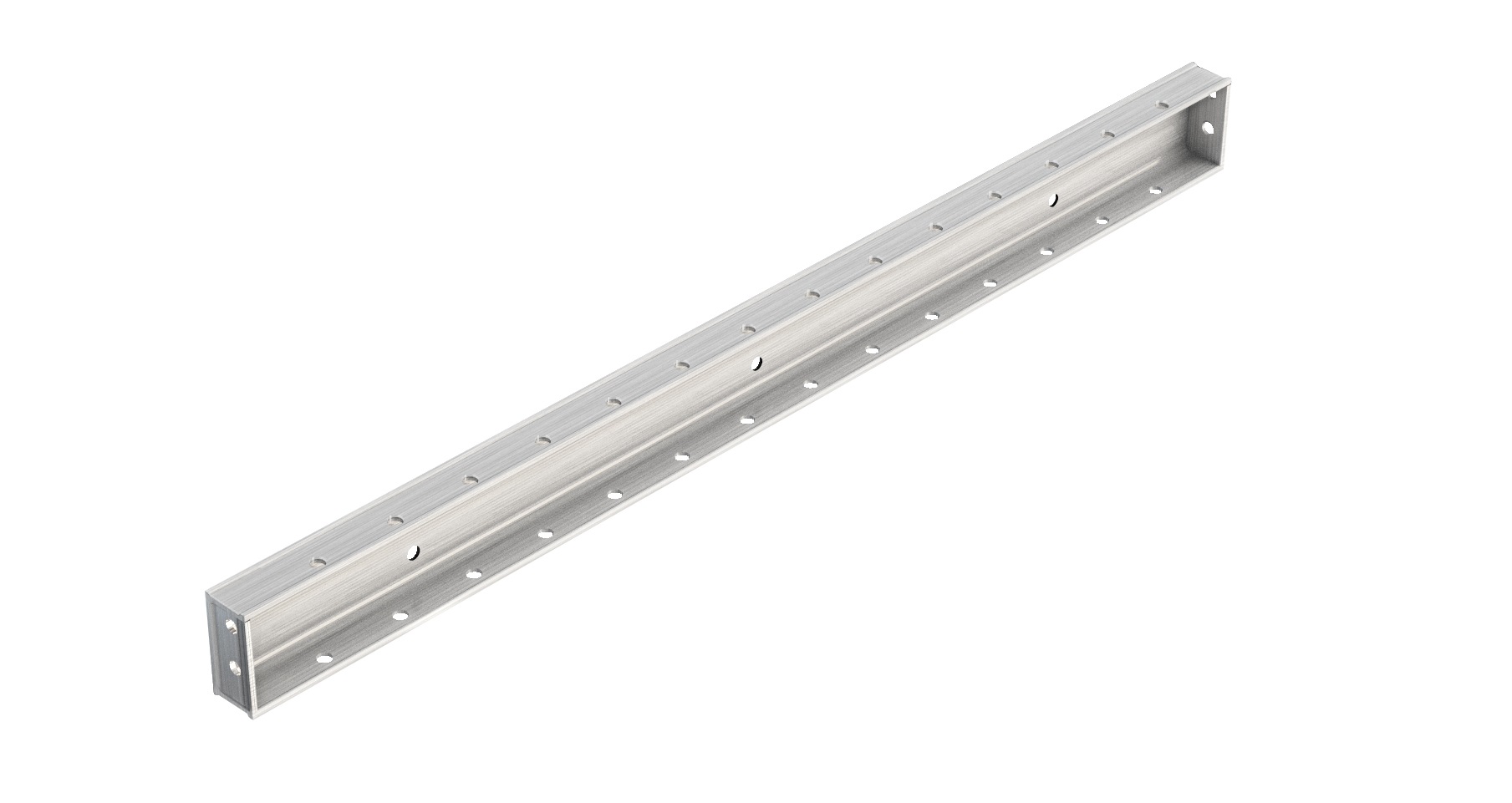
Description | Dimension |
Kicker | 125mm x (L)* |
150mm x (L)* |
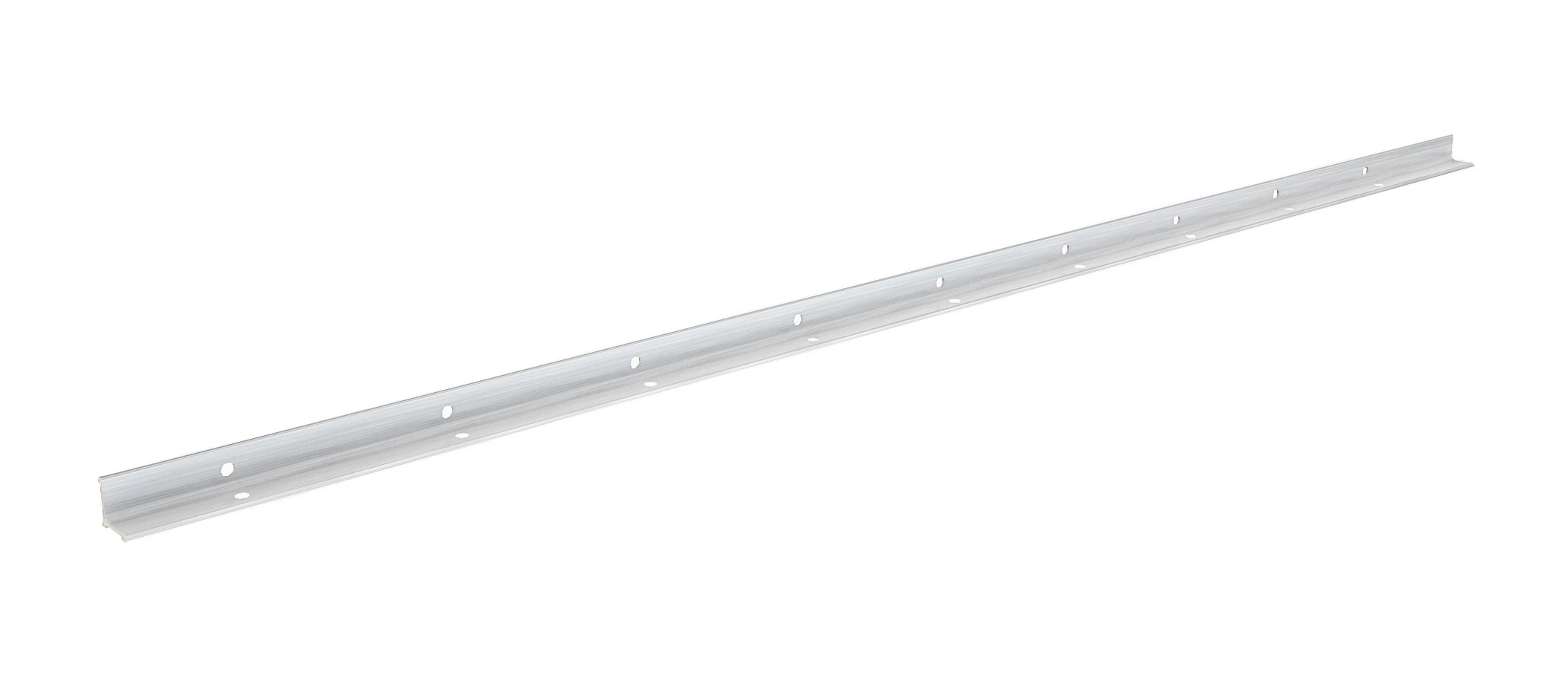
Description | Dimension |
External Corner Angle | 60mm + 60mm x (H)* |
*Height(H) depends on the height of the corner wall panel.
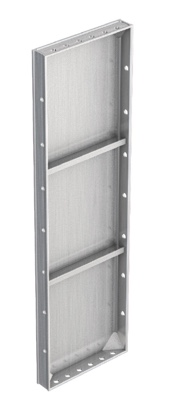
BEAM PANEL is used to support beam side and connects bottom beam panel. Size of beam panel depends on the design requirement.
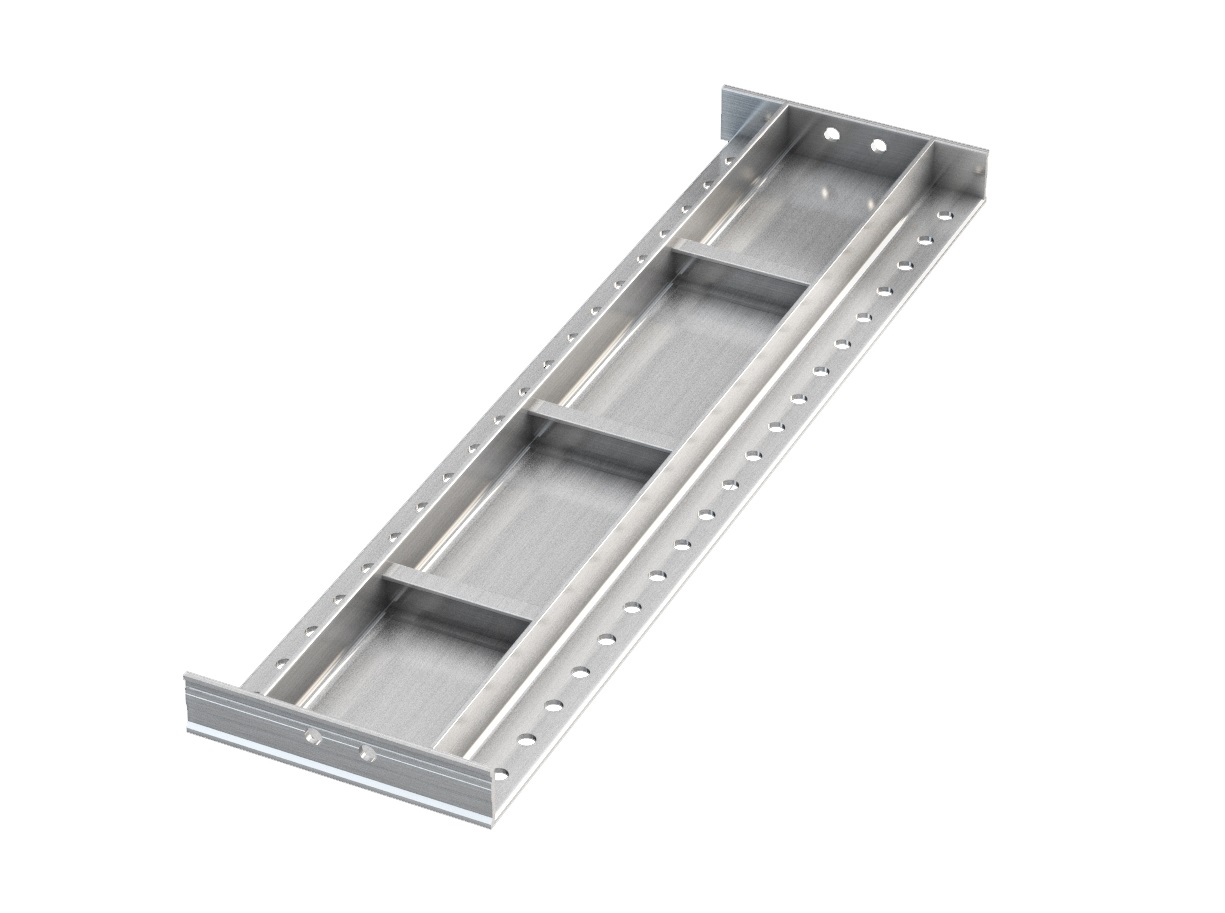
BEAM BOTTOM PANEL is used to form up the beam bottom and used as a window sill cap as well. Size of bottom beam panel depends on the design requirement.
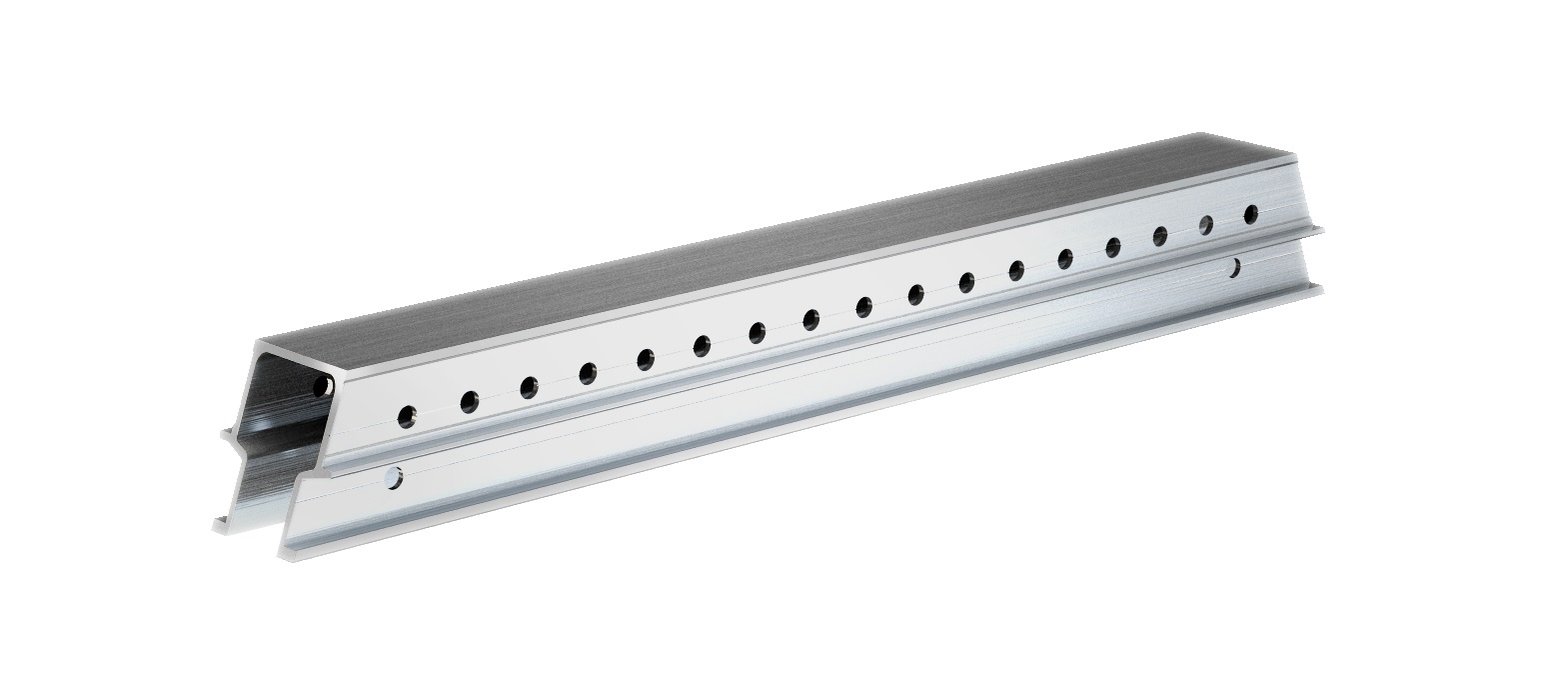
Description | Dimensions |
Standard Middle Beam | 100mm x 900mm |
100mm x 1050mm |
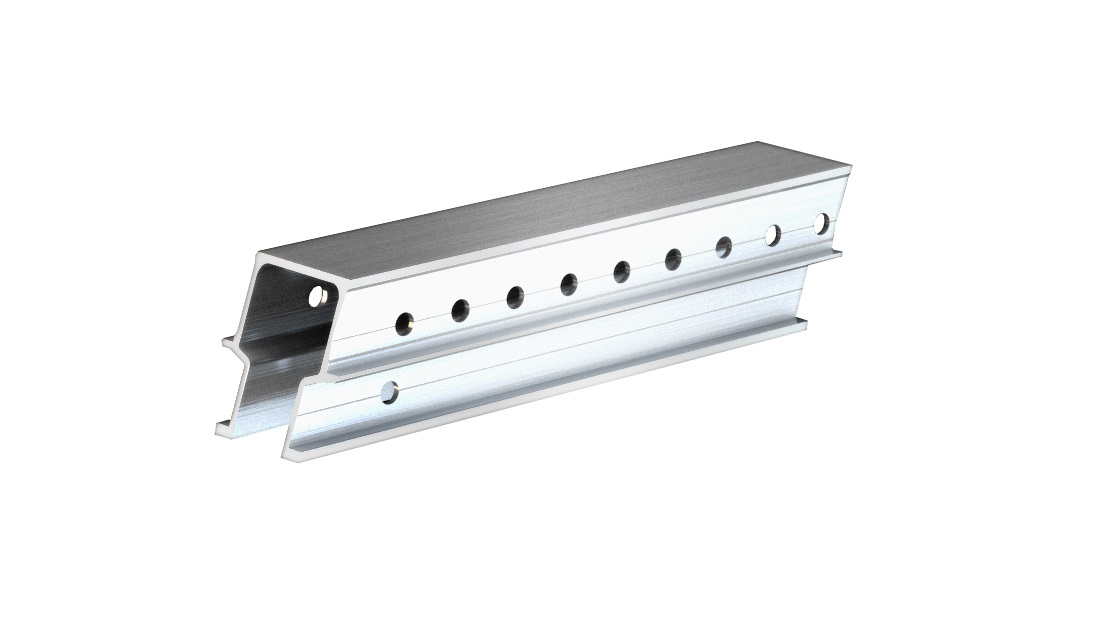
Description | Dimensions |
Standard End Beam | 100mm x 600mm |
100mm x 900mm |
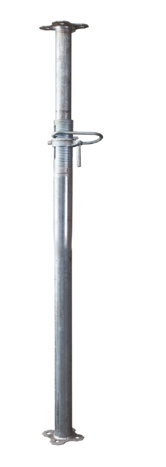
Description | Type | Dimension |
---|---|---|
Adj. Steel Props (Gal.) | V1 |
1800mm~3200mm |
V2 |
2000mm~3400mm | |
V3 |
2400mm~3800mm | |
V4 |
2600mm~4000mm |
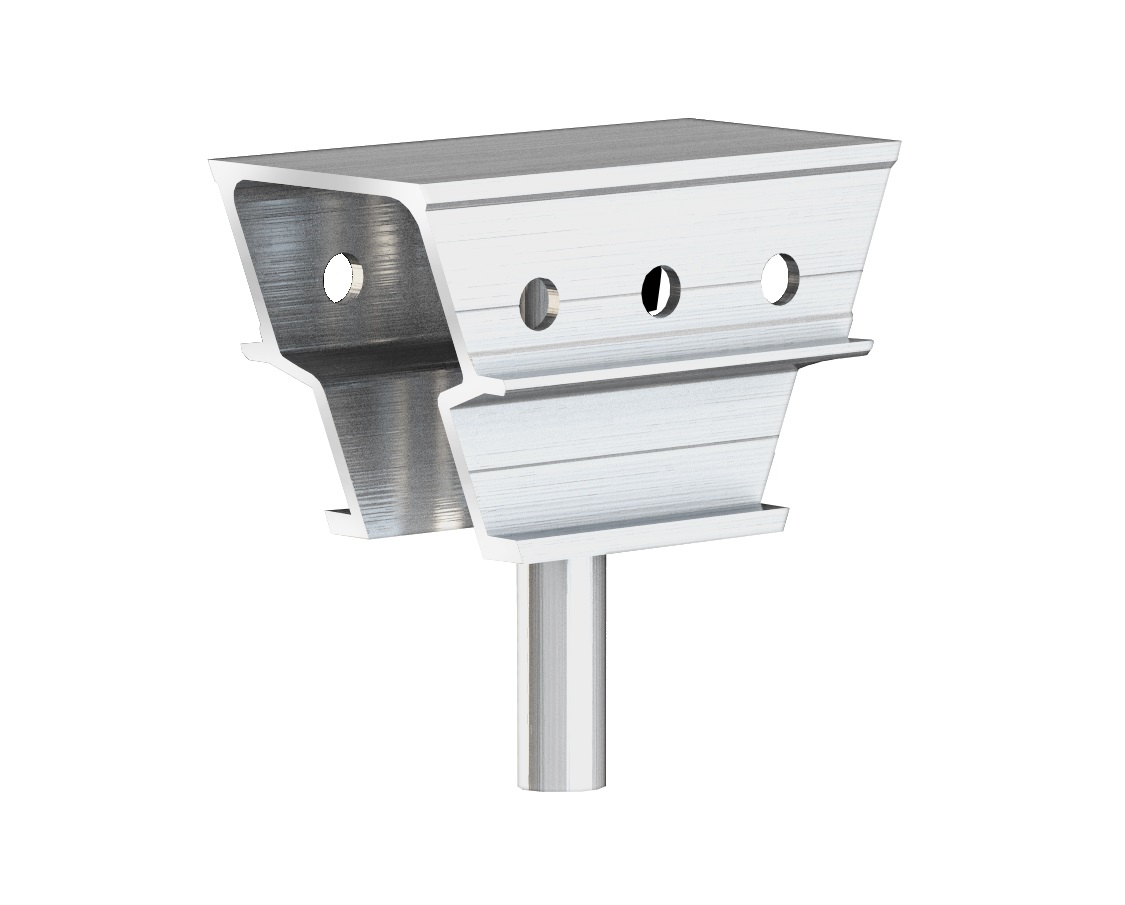
Description | Dimension |
Standard Prop Head | 100mm x 200mm |
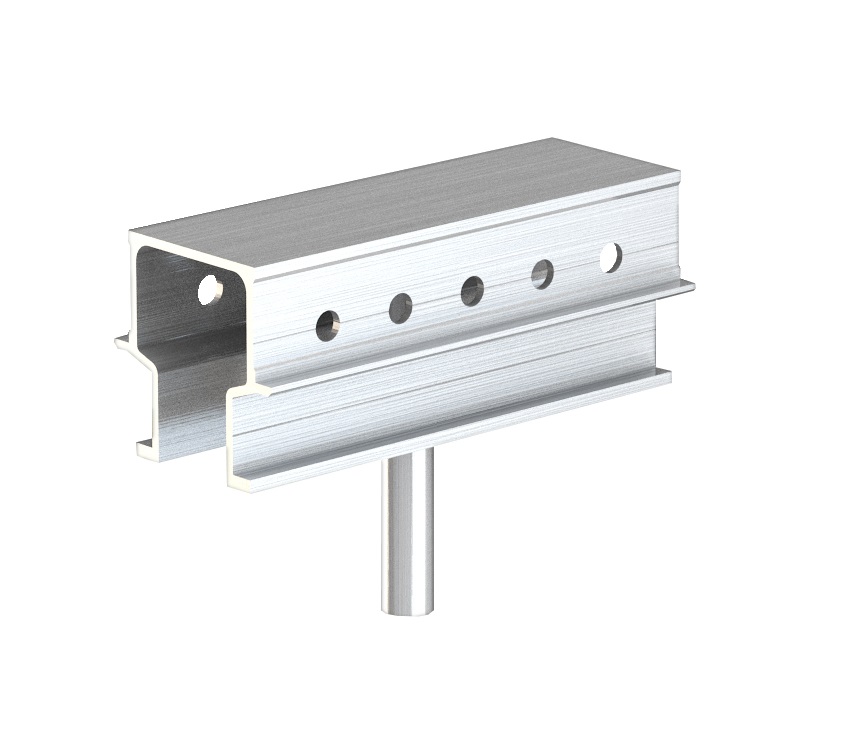
Description | Dimension |
Beam Prop Head | 100mm x (L)* |
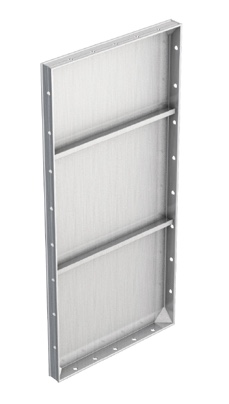
Description | Dimension |
Standard Slab Panel | 600mm x 1300mm |
450mm x 1300mm | |
200mm x 1300mm | |
175mm x 1300mm |
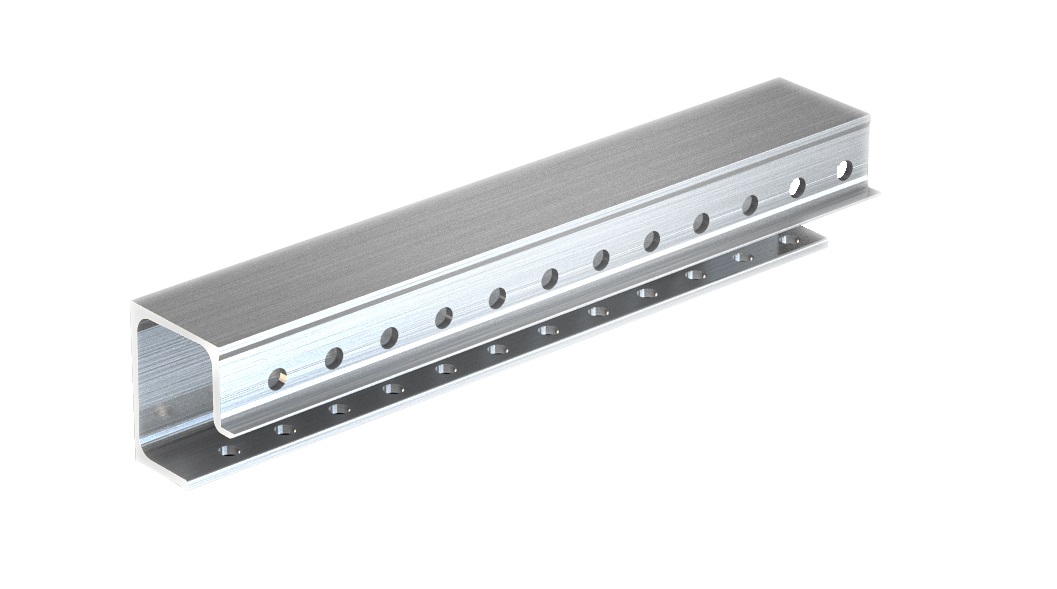
Description | Dimension |
Slab Length | (125mm + 100mmm) x (L)* |
(150mm + 150mm) x (L)* | |
(125mm + 75mm) x (L)* |
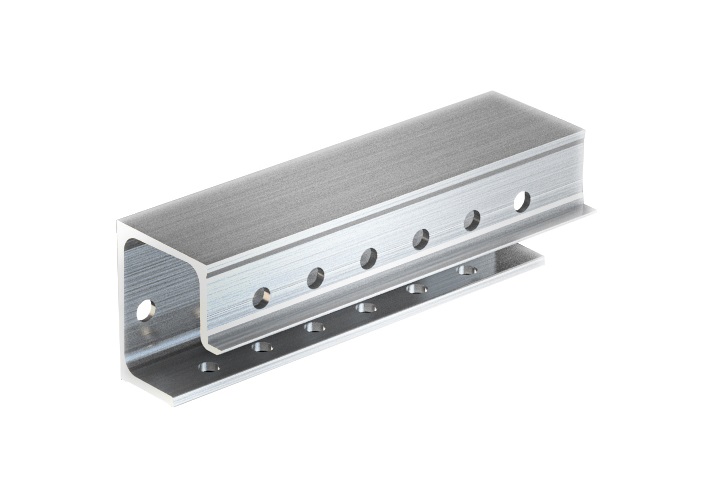
Description | Height |
Corner Collar | 125mm |
150mm |
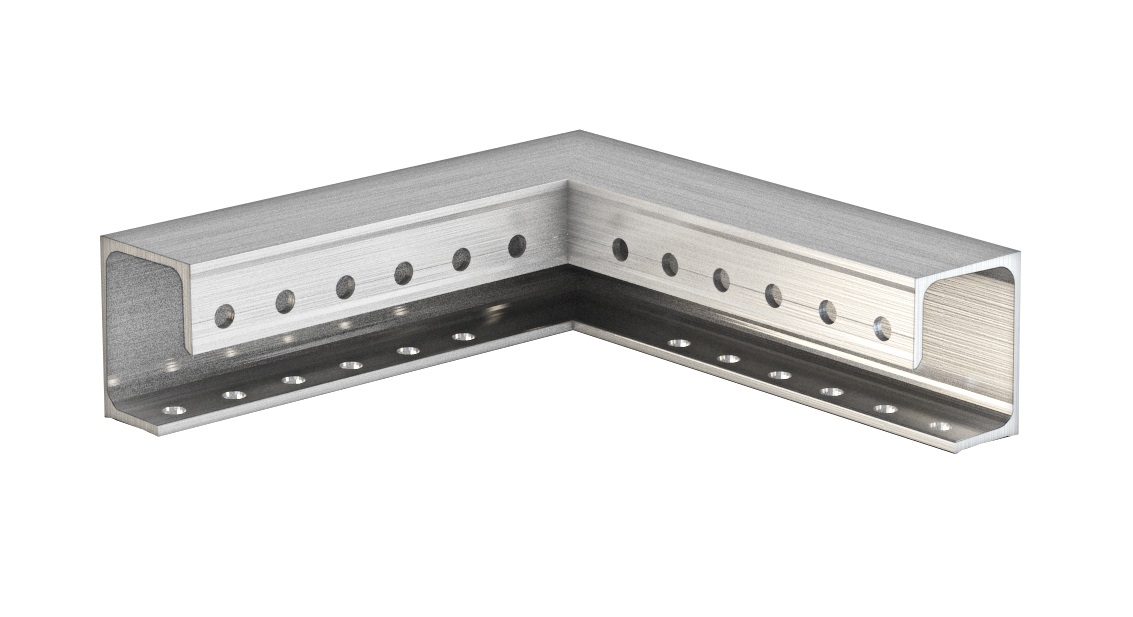
Description | Dimension |
Slab In-Corner | (350mm + 350mm) X 125mm |
(350mm + 350mm) X 150mm |
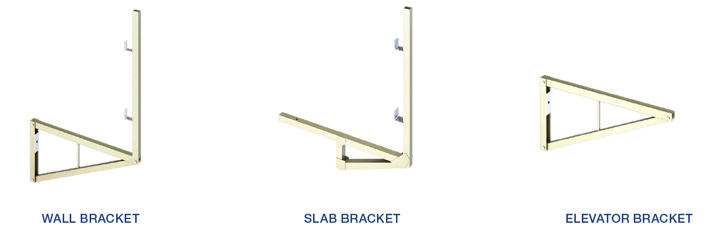
WALL BRACKET& ELEVATOR BRACKET are fixed on the concrete wall and SLAB BRACKET are fixed in the slab concrete after taking off the wall and slab panels. It acts as the working platform on the outer surface of the structure.
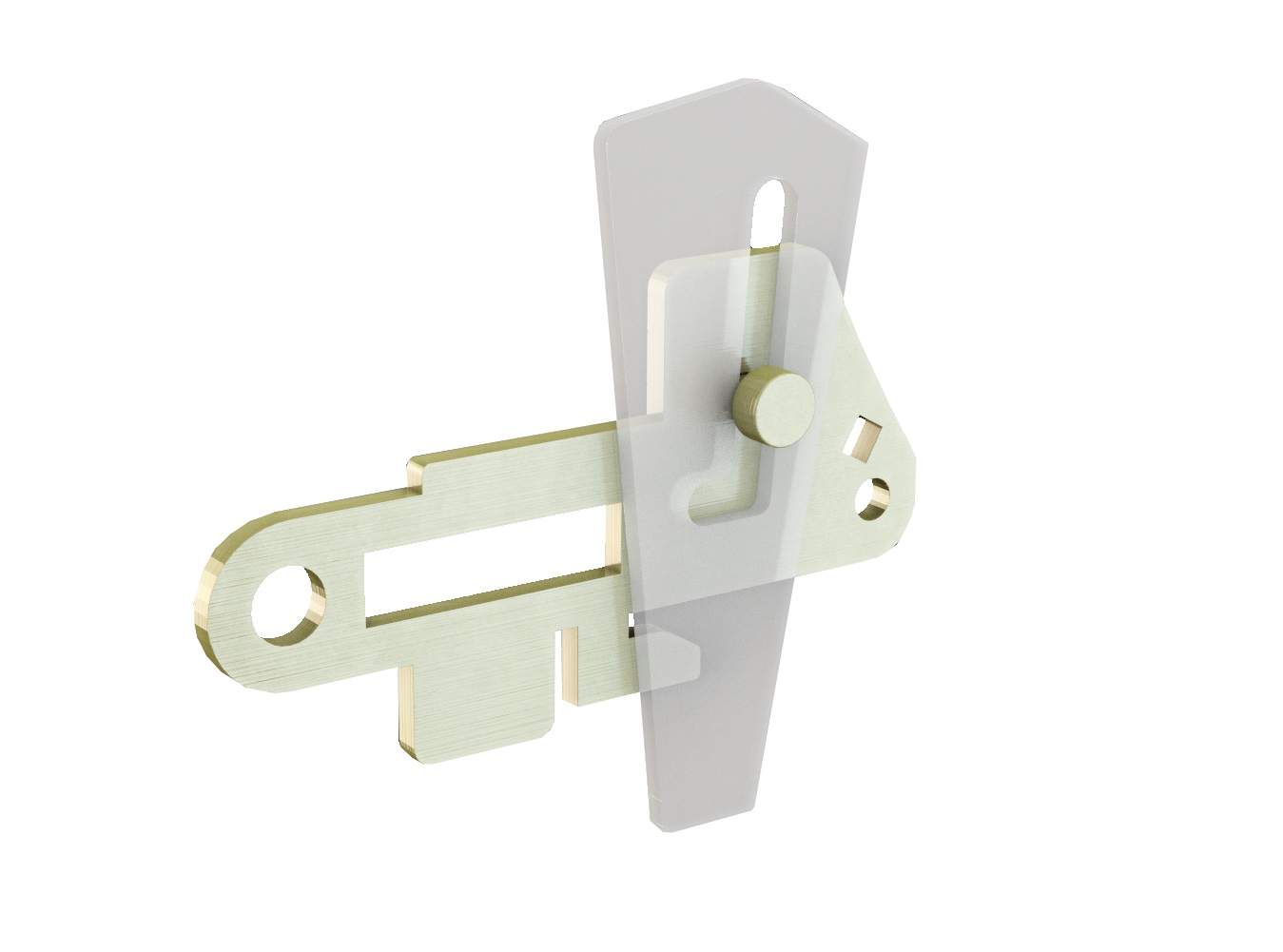
WALLER HOLDER is installed on the bottom of the wall panel surface. It holds a waller pipe to sustain the pressure of concrete to prevent leakage
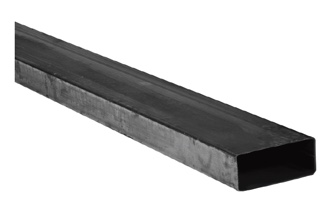
WALLER PIPE is placed on a waller holder to ensure thehorizontal alignment of the structure.
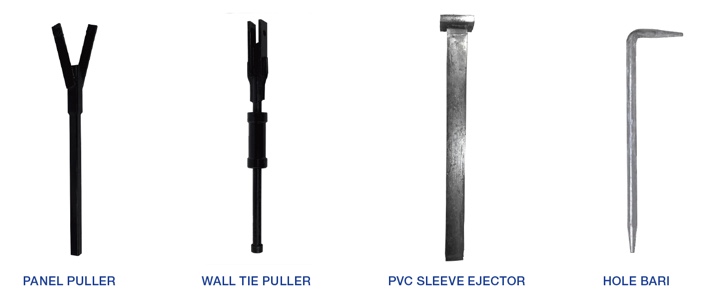
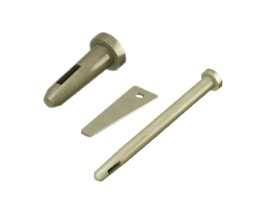
LONG PIN, SHORT PIN & WEDGE PIN are the main accessories to join the panels. It is used to secure and tighten the panel together.
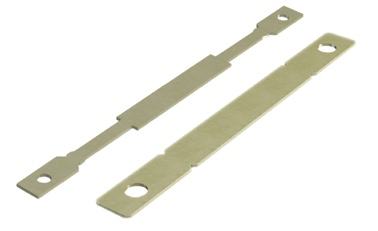
EMBEDDED FLAT TIES are used to join the double-faced panels. Number of wall ties vary, depends on the wall panels height. Exposed portion is broken off after dismantling the wall panel
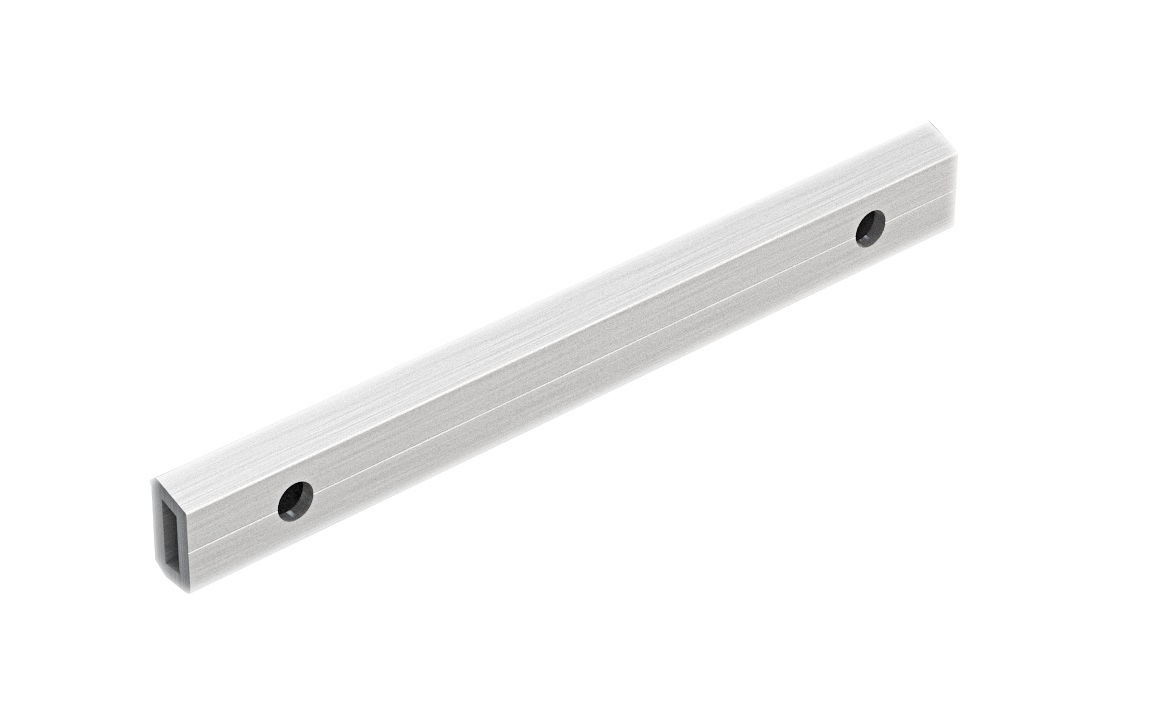
JOINT BAR is used to Join the prop head with the beam (Middle beam/End beam). Long pin and wedge are used as a connection accessories.
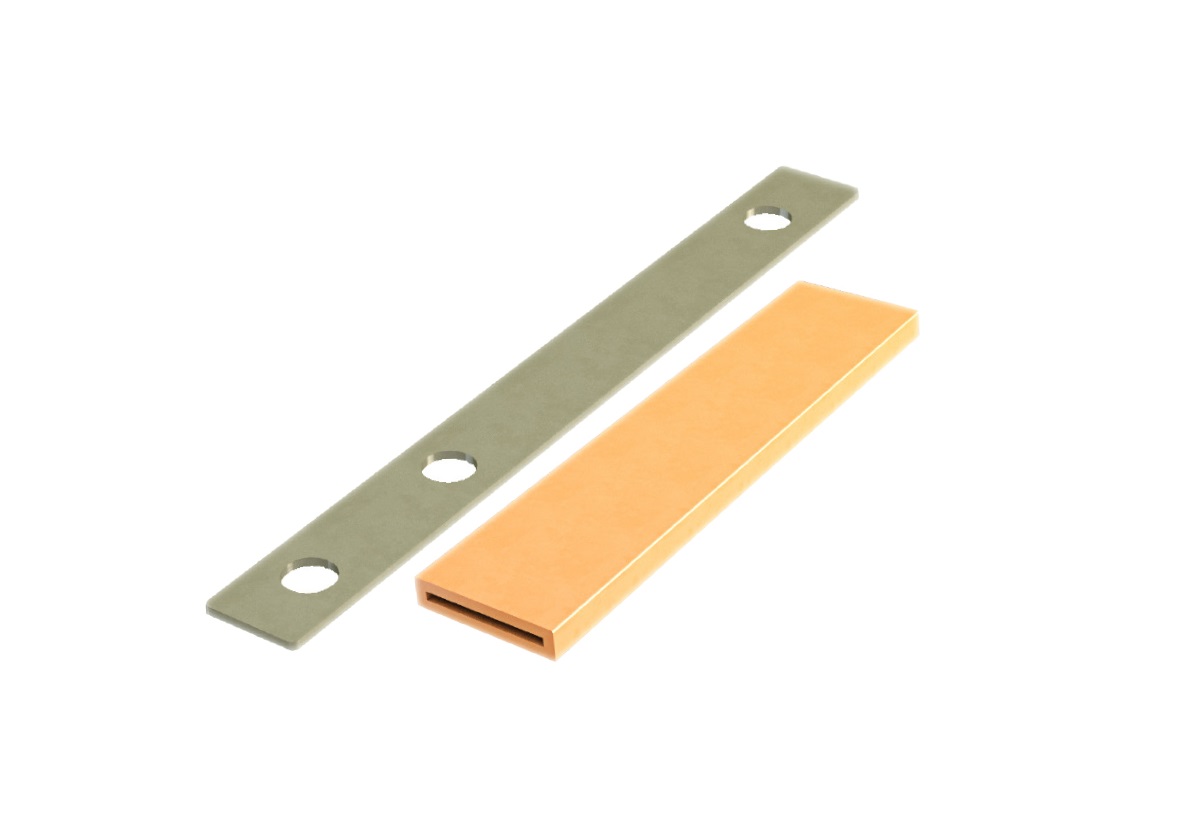
REUSABLE FLAT TIES & PVC SLEEVES are used to joint the double-faced panels. It is used to maintain wall/column thickness as well as resisting concrete pressure. Flat ties are inserted into PVC sleeves for easy removal after casting of concrete. This type of flat ties can be reused number of times with the help of PVC sleeves.
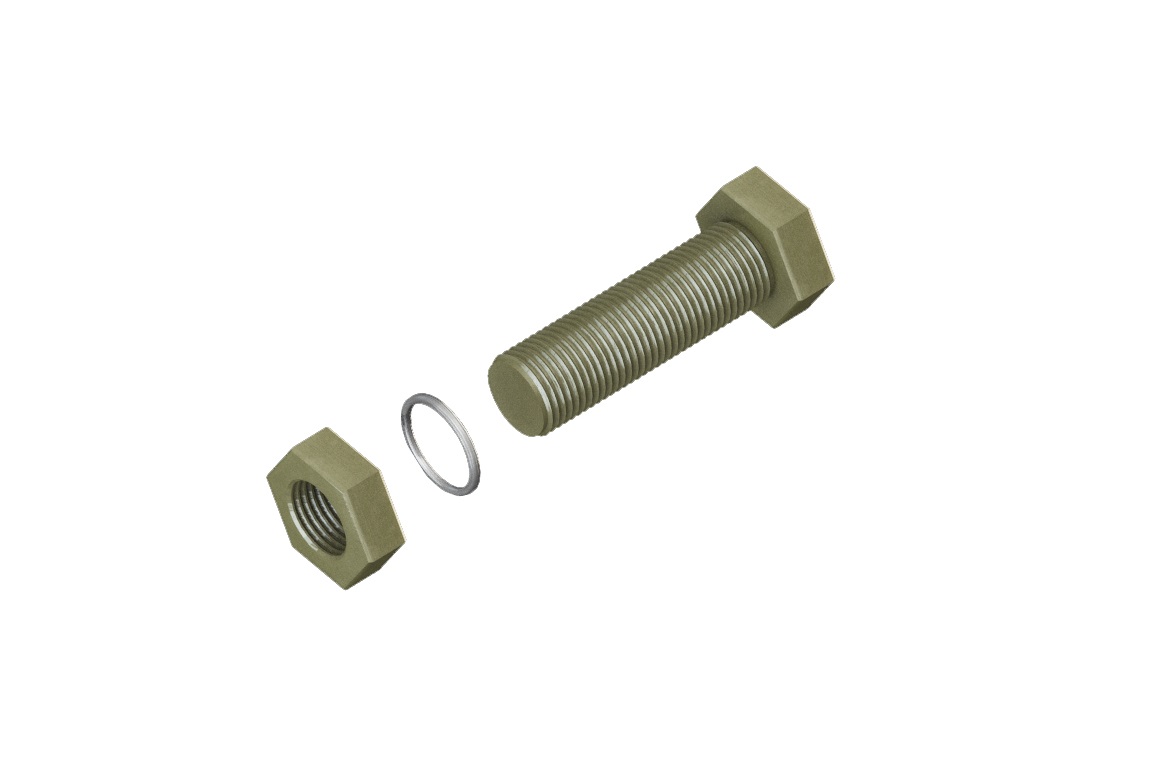
KICKER BOLT, NUT & WASHER are fixed into kicker hole. Bolt can be removed after pouring of concrete and can be reused for next floor.
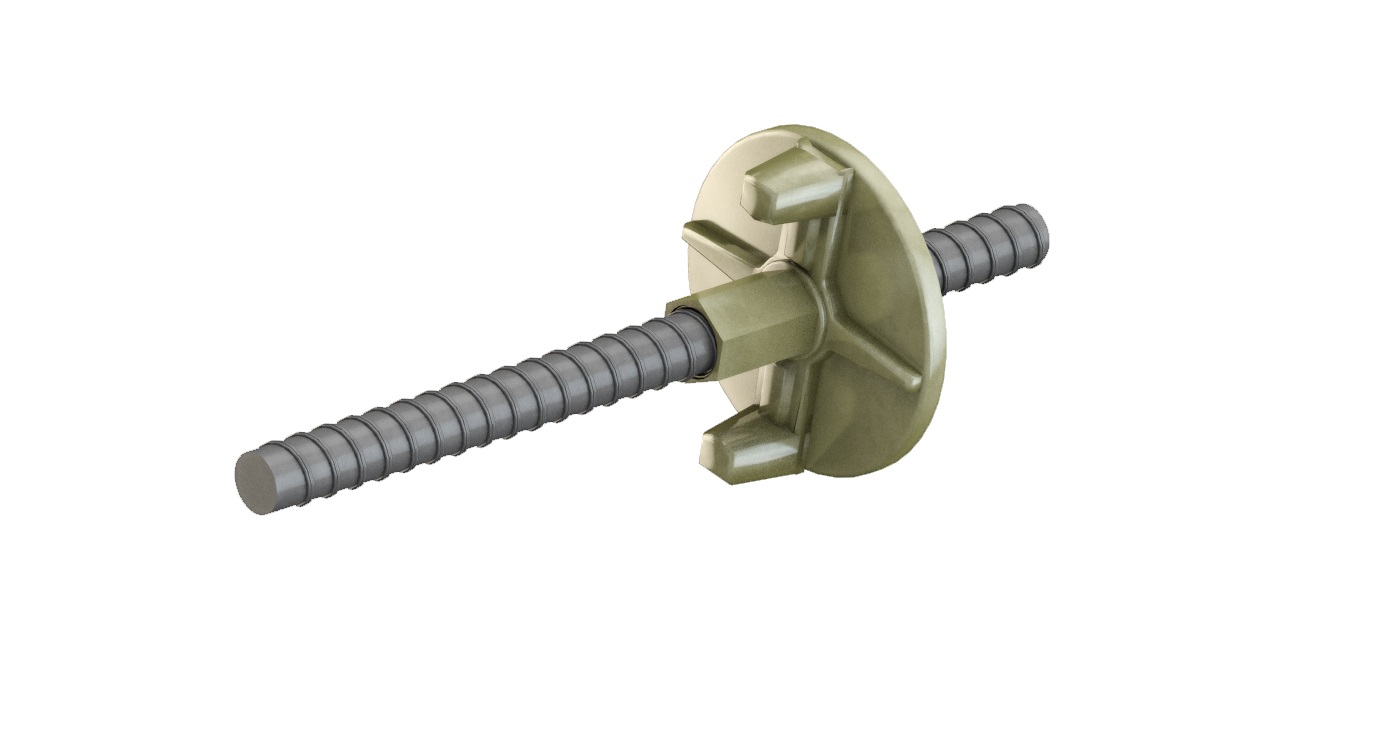